Frequently Asked Questions
If you can’t find what you’re looking for, feel free to reach us in chat, at info@staging-wp.xometry.uk or +44 1245-840035
About Xometry
Xometry is a leading AI-enabled marketplace for on-demand manufacturing, transforming one of the largest industries in the world. Xometry empowers the industries of today and tomorrow by connecting the people with big ideas to the manufacturers who can bring them to life.
Xometry’s digital marketplace gives manufacturers the critical resources they need to grow their business while also making it easy for engineers and purchasers at small and large enterprise companies to tap into global manufacturing capacity and create resilient supply chains.
Although our trademark is an AI-generated instant quotation tool, Xometry’s strength lies in its large team of engineers, production managers, account managers, quality controllers and many others. The Xometry UK team is spread across the four corners of the continent, its official headquarters being in Chelmsford, United Kingdom.
Our teammates are Xometry’s most important asset. The powerful combination of their unique knowledge and abilities drives our company and its marketplace. We embrace both independent thought and teamwork to tackle tough problems, empowering our team to find the best solutions.
Xometry has a team of manufacturing specialists in-house to help you with your manufacturing projects. Xometry also has in-house manufacturing specialists to help customers source suppliers for projects with special requirements and manage suppliers through the manufacturing and delivery process.
We provide manufacturing services for all industries that require metal and polymer custom and serial production parts, amongst which:
- Aerospace
- Automotive
- Consumer goods
- Electronics & Robotics
- Energy
- Engineering
- Machine building
- Medical
The diversity of our services allows us to meet most of your requirements, whatever the application.
Xometry’s customers range from self-funded startups to Fortune 100 companies. Over 40,000 engineers and purchasing leaders from companies like BMW, General Electrics, Dell and Bosch trust our services. Learn more about Xometry’s customers’ success stories.
Xometry helps you save a considerable amount of project time thanks to a powerful combination of the AI-powered Instant Quoting Engine, a massive production network and a dedicated team available at any time during the conception and production processes.
As a customer, you can choose your part’s specifications amongst 15+ technologies, 130+ materials and 40+ finishing options, and get free quotes within a few minutes. Xometry takes care of the rest, from the DFM feedback to the delivery of your parts.
Customers
Our international team speaks many different languages and we do our best to serve our customers in their local languages whenever it is possible. Please note that all the people you might be in touch with from Xometry are also English speakers.
Here is a list of all languages spoken at Xometry:
- English
- German
- French
- Italian
- Spanish
- Portuguese
- Polish
- Dutch
- Finnish
- Russian
- Ukrainian
We take your intellectual property very seriously. Every drawing, sketch or picture you upload to our system is kept completely secure. We use state-of-the-art security algorithms. Traffic at our website is secured by the SHA-256 algorithm with RSA encryption.
Once your order is placed, only the provider who actually manufactures your part has access to the part drawing. All workshops in our network are under contract to protect your IP. If you require a special non-disclosure agreement (NDA), please request it from your dedicated account manager.
Yes. There are two ways for the customer and Xometry to work with a Non-Disclosure Agreement (NDA):
- The customer’s company already has an NDA. The NDA is to be reviewed and signed by Xometry and the customer
- The customer’s company doesn’t have an NDA, in which case Xometry can provide its own NDA. The NDA is then to be reviewed and signed by both parties
Xometry.uk and its CAD add-ins are free to use to get online quotes. The quoted price you see is what you pay, and there are no recurring charges for using Xometry’s services!
Yes. Our instant quoting functions are available for private customers without limitations. You can always get instant quotes with standard quote configuration:
- Manufacturing process: CNC machining, sheet metal fabrication or 3D printing
- File formats: STEP, STP, SLDPRT, STL, SAT, 3DXML, 3MF, PRT, IPT, CATPART, X_T, PTC, X_B + DXF (for sheet cutting)
- Line item value: up to €7,000
- Line item quantity: up to 1,000 pcs
- Standard material and finishing: Hundreds of combinations available in the Instant Quoting Engine®
However, there are some cases when a manual project review by our engineers or placing team is needed. It is only available for corporate accounts, so individual customers cannot perform the following actions:
- Quote 2D drawings. Technical drawings can’t be instantly quoted by the Instant Quoting Engine and require a manual review.
- Request custom features for your parts.
Please note that since you won’t have a corporate account, you will have to pre-pay all your orders.
When a customer reports a complaint or a claim, the Xometry Production Team handles the case and starts investigating. A case engineer specialising in the manufacturing process with which the part was produced will examine the case together with our QC engineers to determine the issue. Once the case is examined, Xometry offers a viable solution to the customer.
Overall, Xometry targets to build long-term relationships with our customers and is set to find solutions for each claim or issue with our customers’ orders.
Manufacturing Capacities
We offer over 15 manufacturing processes:
- CNC machining (milling, turning, drilling)
- Sheet metal fabrication (laser, plasma waterjet cutting and bending)
- 3D printing (HP MJF, FDM, SLS, SLA, DMLS, Carbon DLS, Polyjet)
- Injection moulding (injection moulding, overmoulding, insert moulding)
- Die casting
- Vacuum casting
- Compression moulding
For any custom requests, reach out to your assigned sales representative or contact us at info@staging-wp.xometry.uk.
If you have trouble figuring out which manufacturing process is the most suitable for your project, you can refer to our manufacturing technology selection guide and our 3D printing process and material decision guide. You can also ask for the advice of your assigned sales representative.
Xometry UK offers a wide selection of over 130 common metals and plastics as well as custom and rare materials. In the Instant Quoting Engine, you can choose material from the list or type the name of the custom material your project requires.
Find more information in our material section.
Xometry has built a manufacturing network of over 10,000 manufacturing partners globally. In addition to it, we use advanced IT technologies that allow us to efficiently manage our manufacturing network and place production jobs. Such a scale and the use of modern technologies allow us to always offer reasonable lead times that are competitive with conventional ways of sourcing parts.
Xometry does not own its own workshops, but we do have a massive manufacturing network worldwide with over 10,000 partners, amongst which more than 2,000 are located in Europe only. Xometry consolidates the supply chain by having a single storefront for multiple manufacturing options, while also mitigating any risk associated with sourcing through its 10,000+ manufacturer marketplace.
The parts you order are sent through Xometry’s Manufacturing Partner Network. This is a vetted network of professional manufacturers from job shops to serialized production facilities. Xometry uses its AI-driven technology to pair projects with those manufacturers best suited to produce the parts on time and to your requirements.
Once you place an order in the Xometry Instant Quoting Engine®, we will find the most optimal partner to manufacture your parts. Optimal partners are workshops with the right capabilities and availability for your project, who can start working on your order immediately. These workshops are located all over Europe, but also in Turkey and China.
In case of repeated orders, we ensure that the batches of parts will be manufactured by the same provider, subject to the availability of the latter.
Yes. Xometry is a production powerhouse with a global network capacity of 10,000+ facilities, 2,000+ of which are located in Europe. We’re ready to take on jobs of any size, from a single part to one million parts, for CNC machining, sheet metal fabrication, injection moulding, vacuum casting, compression moulding, die casting and 3D printing.
Our strength lies in our ability to allocate orders according to the capacities and availability of our massive network of suppliers. We ensure affordability, quality of manufacturing and quality of service. We also provide account management, in-house engineering support, and in-house quality control teams working for our customers.
Learn more about our high-volume manufacturing capacities.
Materials & Specifications
We work with both custom and general tolerances: ISO 2768 (fine, medium) and ISO 286 (Grades 8, 7, 6) for CNC machining and sheet metal fabrication. Learn more about subtractive manufacturing standard tolerances.
Even though there are no international standards on tolerances for 3D printing, tolerances play a key role in the final dimensions of the part. In 3D printing, the major factors influencing the tolerances are material shrinkage (change in volume from a change in state from liquid to solid), layer thickness minimum feature size and build size (maximum size of the part to be printed, depending on the technology). Learn more about the tolerances applied to each 3D printing process.
As far as formative technologies are concerned, we work according to the following standards: DIN 16742 for injection moulding and compression moulding, and ISO 8062 for die casting. As for vacuum casting, a standard ±0.5 mm is usually applied. Tighter tolerances are upon request.
Xometry offers a wide range of materials with different aesthetic and mechanical properties. Check our material selection for all manufacturing technologies.
If you’re looking for specific materials for 3D printing, you can find a list of materials depending on their properties in the following list:
Quoting & Ordering Options
From your dashboard, you have access to three distinct quoting & ordering options, each tailored for different project needs:
- Instant Quoting Engine: Ideal for prototypes and small-to-mid-sized batches, this tool provides instant quotes for CNC machining, sheet metal fabrication, 3D printing, and vacuum casting.
- Mid & High-Volume Manufacturing Quotes: Perfect for managing complex projects, including assembly, welding, and framework production with scheduled batch shipments, this option is available to our corporate customers.
- Target Price Orders: Designed for our corporate customers, this option allows you to source parts at your own price—a perfect solution for mid- and high-volume projects where budget control is crucial.
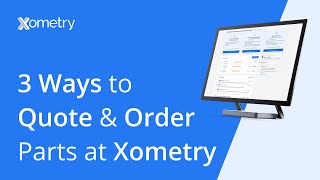
To get an instant quote, follow the step-by-step instructions below:
- Start by uploading one or multiple CAD files. Our advanced algorithms will analyze each model’s geometry, delivering instant price estimates and available lead times.
- To refine your quote, click ‘Edit Specifications.’ Here, you can adjust the process, material, quantity, finishing, and other parameters, with the price updating automatically based on your changes.
- Additionally, you can select the required tolerances and, if necessary, specify the number of threads and tapped holes. In this case, you’ll need to upload an additional drawing. You can also enter any additional project requirements for the engineers and manufacturers in the provided text field.
- Once you’ve finished editing the part specifications, return to the quote page to add more parts if needed.
- Here, you can also specify the required certifications. When your quote is finalized, proceed to checkout. If you haven’t already added your shipping address, you can do so to calculate the shipping costs.
- Proceed to payment using a variety of methods, including PayPal, bank card, proforma invoice, or other country-specific options.
- Your order is now being processed, and production will begin shortly.
To get a mid and high-volume quote, follow the step-by-step instructions below:
- Start by uploading your project files—CAD designs, technical drawings, or even Excel files. If your files contain all the necessary production details, simply activate the relevant toggle and click ‘Review & Confirm’ to request the quote, allowing our team to immediately begin processing your project specifications. Otherwise, enter your project requirements in the provided text field. You can use our template or type your specifications from scratch.
- For scheduled shipments, specify your desired schedule.
- When you’re ready, click ‘Review & Confirm’ to double-check your files and entered information.
Proceed by clicking the “Request Quote” button. Within 24-48 hours, our pricing engineers will prepare a comprehensive quote tailored to your project specifications. The quote will be organized into a clear part-by-part interface. - You can then place your order as easily as with an instant AI-generated quote.
Our Instant Quoting Engine provides quotes with price and delivery time within a few seconds for CNC machining, sheet metal fabrication and 3D printing quotes. For injection moulding, die casting, vacuum casting and compression moulding projects, you can request a manual quote. These are usually provided within 24-48 hours. Manual quotes are available for corporate customers only.
If you are not satisfied with the given price, you can always reach out to your sales representative to discuss the quotes generated by the Instant Quoting Engine.
Payment & Delivery
To be able to place an order at Xometry, its value should exceed or be equal to 100£.
We accept payments by credit cards, PayPal, Sofort, invoices (bank transfer) and others.
The delivery time is indicated in the Instant Quoting Engine interface, in the top-right corner of your screen. It depends on the chosen delivery option (standard or express, when available). Please note that the date shown is the date on which the order will be dispatched from the point of production.
Please note that the delivery time of your quote might evolve depending on your actions in the interface (change of technology of materials, addition of post-processings, change of quantity, etc.). The actual delivery time is the one displayed once all the changes have been made and once the order is placed.
CAD Designs
The Xometry Instant Quoting Engine can automatically quote thousands of different shapes, features, and configurations! To do it needs a suitable file type:
- If the computational geometry algorithms of the Instant Quoting Engine can analyse your part geometry, it will be able to give you an instant quote.
- If the algorithms cannot analyse your design, the line item quantity or value is high, or you added custom features, your part will require additional review by our engineers.
File types & requirements for getting instant quotes
Our Instant Quoting Engine supports all popular CAD files (STEP, STP, SLDPRT, STL, IPT, 3DXML, CATPART, PTC, PRT, SAT and DXF). You can also submit PDF files for technical drawings or quotes for formative manufacturing technologies.
- Solid/Parasolid file types like STEP, SLDPRT, IPT, PRT and SAT can quote in any process.
- Mesh-based formats like STL, 3MF, and 3DXML can quote 3D printing services.
- 2D X_B and DXF files are specific to sheet cutting services.
- Model-Based Definition (MBD) or Part Modeling Information (PMI) is not supported at this time and should be captured with an attached technical drawing on the quote.
- Upper-level assembly files can be uploaded in an STP format but will require individual part files uploaded for quoting. Native CAD assembly files like SLDASM and IAM do not have solid model information and will not load on Xometry’s platform.
- Please remove or suppress any multi-body features, such as installed inserts, before uploading part models.
File types for can be quoted manually
If you only have technical drawings you can also upload them to the Instant Quoting Engine. In this case, you can configure the project requirements, specifying all necessary parameters – quantities, materials, finishing options etc. – and request a manual quote. File types that the platform supports: DWS, DWF, DWG, PDF.
Please note that without a 3D model, the system won’t be able to deliver an automatic quote. Photos, hand drawings and other files that are not 3D files will not be automatically quoted.
No, we don’t provide CAD drafting services.
Quality Assurance & Control
Xometry utilises rigorous processes to ensure the highest manufacturing standards for your custom parts, inspecting dimensions and visual aspects both during and after production to deliver on-time and precisely tailored components. Xometry’s quality management processes are ISO 9001 certified.
We ensure quality through:
- Only working with the best suppliers on the market
- A scoring system for our manufacturing partners
- Clear QA instructions & standards for the manufacturing facilities
- Our own QC lab & QC team for complex and critical parts
- External QC labs
If you require quality control reports – please specify the certifications you need in your enquiry. Typically, the control procedures could be supported by material certificates, conformity certificates, and reports of inspections. Please make sure to specify the quality control procedures before placing the order – introducing them once the production has started is very difficult.
Yes, standard quality control of the part is done onsite by the manufacturer. For each order, partners are required to take pictures of the parts and upload them to the platform before sending out the parcel.
Parts can also be controlled by external QA labs in order to confirm specific properties (e.g. material composition, high accuracy dimensions, quality of welds, etc.) for an additional cost.
Yes. The following quality documents can be purchased for all our manufacturing technologies (CNC machining, sheet metal fabrication, 3D printing, injection moulding, die casting, vacuum casting and compression moulding):
- CMM Inspection Report
- Material Certificate (for metals only)
- Standard Measurement Protocol
- First Article Inspection Report (FAIR)
- RoHS (Restriction of Hazardous Substances Directive)
- REACH (Registration, Evaluation, Authorisation and Restriction of Chemicals)
- Certificate of Conformance
Our production partners are the key to ensuring the quality of our parts. That’s why we apply a strict selection process to ensure that we only work with the best manufacturers on the market.
- A scoring system for existing partners: Once in our network, manufacturers are closely monitored and rated as they fulfil production jobs. This scoring system affects the extent of our collaboration since a higher rating generally leads to more orders being placed. Our partners, therefore, carry out full quality control, as the quality of the parts they produce directly impacts their score.
- A quality control procedure for new partners: To join the Xometry Partner Network, a manufacturer had to prove it meets our standards and requirements with a test order. When a test order is delivered to our office from a partner, we control the packaging and check the order documents to ensure compliance with the order specs in our system. The test part is then checked by the Xometry Quality Assurance Lab (visual inspection, material inspection, dimensional measurement)
- If there is an issue at any of these stages, the partner unfortunately cannot work with us.
Only 35% of all test orders successfully pass our quality control step.